EWD – Effluent & Water Division - Water Treatment
Water treatment is any process that improves the quality of water to make it more acceptable for a specific end-use. The end use may be drinking, industrial water supply, irrigation, river flow maintenance, water recreation or many other uses, including being safely returned to the environment. Water treatment removes contaminants and undesirable components, or reduces their concentration so that the water becomes fit for its desired end-use. This treatment is crucial to human health and allows humans to benefit from both drinking and irrigation use.
'Ultra-Pure Water' (UPW) Plant is our signature offering, which is used in semiconductor industry, pharmaceutical industry and the sectors that have specific requirements w.r.t Conductivity, Microbes, TOC, etc. to be controlled with clear-cut deadlines on upper limit.
We have developed a Reverse Osmosis Plant, for industrial polishing treatment, in compliance with stringent industrial quality standards. These plants are used in laboratories & for Kidney Dialysis.
Multi Grade Filter
A most recent idea in the water treatment innovation, a Multi Grade Filter comprises of vertical or flat weight sand filters that contain various layers of coarse and fine sand (stones and rock) in a fixed extent.
It is a sort of a profound filter bed with satisfactory pore measurements for holding both vast and little suspended solids and un-broke down contaminations like residue particles.
When contrasted with regular sand water filter, this multi grade filtration framework chips away at higher explicit flow rates. It is additionally a minimal cost pre-treatment framework for ion exchangers (deionizer and softener) and membrane systems, for example, reverse osmosis and so forth.
The working principle of a multi grade filter is very straight forward. In a multi grade filter or pressure sand filter, water is gone through multi layers of filter media comprising reviewed sand, rocks and rock layers. The contaminants in the water are caught in the media bed and sifted water goes into the release manifold at the base of the tanks. The following step is discharging, a procedure of adequately expulsion of caught contaminants from the media bed. After back washing, the filter is flushed with raw water and after the required nature of water is accomplished the filter is returned to support.
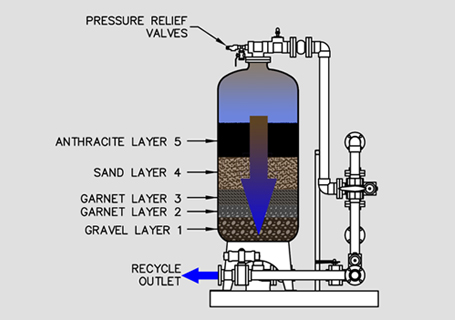
Activated Carbon Filter
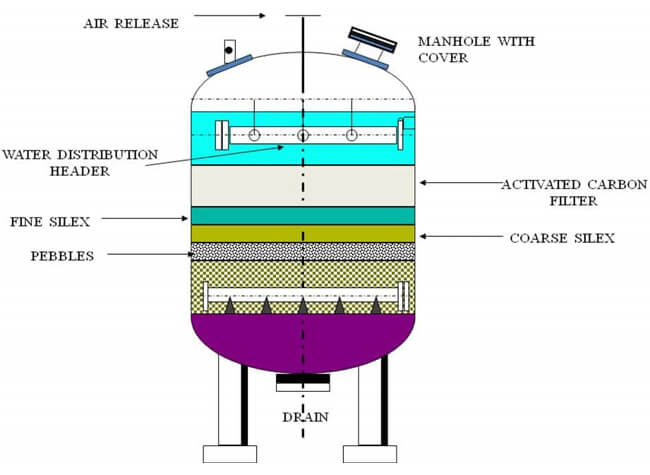
Carbon filtering is a method of filtering that uses a bed of activated carbon to remove contaminants and impurities, using chemical adsorption.
Each particle, or granule, of carbon provides a large surface area, or pore structure, allowing contaminants the maximum possible exposure to the active sites within the filter media. One gram of activated carbon has a surface area in excess of 3,000 m2 (32,000 sq. ft).
Activated carbon works via a process called adsorption, whereby pollutant molecules in the fluid to be treated are trapped inside the pore structure of the carbon substrate. Carbon filtering is commonly used for water purification, air filtering and industrial gas processing, for example the removal of siloxanes and hydrogen sulfide from biogas. It is also used in a number of other applications, including respirator masks, the purification of sugarcane and in the recovery of precious metals, especially gold. It is also used in cigarette filters and in the EVAP used in cars.
Active charcoal carbon filters are most effective at removing chlorine, particles such as sediment, volatile organic compounds (VOCs), taste and odor from water. They are not effective at removing minerals, salts, and dissolved inorganic substances.
Typical particle sizes that can be removed by carbon filters range from 0.5 to 50 micrometers. The particle size will be used as part of the filter description. The efficacy of a carbon filter is also based upon the flow rate regulation. When the water is allowed to flow through the filter at a slower rate, the contaminants are exposed to the filter media for a longer amount of time.
Water Softening Plant
Water softening is the removal of calcium, magnesium, and certain other metal cations in hard water. The resulting soft water requires less soap for the same cleaning effort, as soap is not wasted mopping up calcium ions. Soft water also extends the lifetime of plumbing by reducing or eliminating scale build-up in pipes and fittings. Water softening is usually achieved using lime softening or ion-exchange resins but is increasingly being accomplished using nanofiltration or reverse osmosis membranes.
Microfiltration
Microfiltration is a type of physical filtration process where a contaminated fluid is passed through a special pore-sized membrane to separate microorganisms and suspended particles from process liquid. It is commonly used in conjunction with various other separation processes such as ultrafiltration and reverse osmosis to provide a product stream which is free of undesired contaminants.
Microfiltration usually serves as a pre-treatment for other separation processes such as ultrafiltration, and a post-treatment for granular media filtration. The typical particle size used for microfiltration ranges from about 0.1 to 10 µm. In terms of approximate molecular weight these membranes can separate macromolecules of molecular weights generally less than 100,000 g/mol. The filters used in the microfiltration process are specially designed to prevent particles such as, sediment, algae, protozoa or large bacteria from passing through a specially designed filter. More microscopic, atomic or ionic materials such as water (H2O), monovalent species such as Sodium (Na+) or Chloride (Cl−) ions, dissolved or natural organic matter, and small colloids and viruses will still be able to pass through the filter.
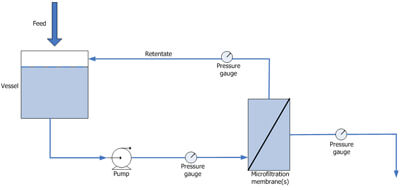
Nano Filtration
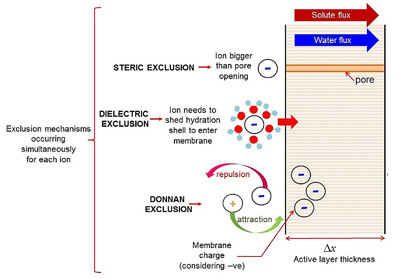
Nanofiltration (NF) is a relatively recent membrane filtration process used most often with low total dissolved solids water such as surface water and fresh groundwater, with the purpose of softening (polyvalent cation removal) and removal of disinfection by-product precursors such as natural organic matter and synthetic organic matter.
Nanofiltration is also becoming more widely used in food processing applications such as dairy, for simultaneous concentration and partial (monovalent ion) demineralization.
Ultrafiltration
Ultrafiltration (UF) is a variety of membrane filtration in which forces like pressure or concentration gradients lead to a separation through a semipermeable membrane. Suspended solids and solutes of high molecular weight are retained in the so-called retentate, while water and low molecular weight solutes pass through the membrane in the permeate (filtrate). This separation process is used in industry and research for purifying and concentrating macromolecular (103 - 106 Da) solutions, especially protein solutions.
Ultrafiltration is not fundamentally different from microfiltration. Both of these separate based on size exclusion or particle capture. It is fundamentally different from membrane gas separation, which separate based on different amounts of absorption and different rates of diffusion. Ultrafiltration membranes are defined by the molecular weight cut-off (MWCO) of the membrane used. Ultrafiltration is applied in cross-flow or dead-end mode.
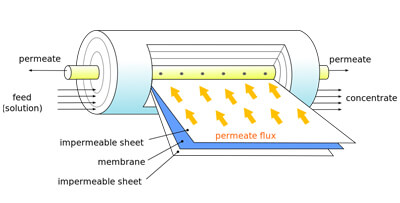
Reverse Osmosis Plant
A reverse osmosis plant is a manufacturing plant where the process of reverse osmosis takes place. An average modern reverse osmosis plant needs six kilowatt-hours of electricity to desalinate one cubic meter of water. The process also results in an amount of salty briny waste. The challenge for these plants is to find ways to reduce energy consumption, use sustainable energy sources, improve the process of desalination and to innovate in the area of waste management to deal with the waste. Self-contained water treatment plants using reverse osmosis, called reverse osmosis water purification units, are normally used in a military context.
Hydro Pneumatic System
A hydro pneumatic system is a machine which will increase the pressure of a fluid. They may be used with liquids. On new construction and retrofit projects, water pressure booster pumps are used to provide adequate water pressure to upper floors of high-rise buildings. The need for a water pressure booster pump can also arise after the installation of a backflow prevention device (BFP), which is currently mandated in many municipalities to protect the public water supplies from contaminants within a building entering the public water supply. The use of BFPs began after The Clean Water Act was passed. These devices can cause a loss of 12 PSI, and can cause flushometers on upper floors not to work properly. After pipes have been in service for an extended period, scale can build up on the inside surfaces which will cause a pressure drop when the water flows.